The Beginning
The construction sector has traditionally been a labour-intensive industry and has in the past exhibited an entrenched resistance to technological adoption. Across industries, we have witnessed a paradigm shift in the last decade in terms of productivity, the speed of which has no historical precedence.
Whilst the exponential pace of technological implementation and adoption is like no other point in time, in comparison the construction industry has only seen a global labour-productivity of an averaged 1% per annum over the past two decades. However, this global transformation will inevitably shape the future of the construction industry.
In Singapore, where many initiatives are government-led, the Building Control (Buildability and Productivity) Regulations 2011 came into operation on 15 July 2011. These Regulations tightened the original requirements under the Buildability Design Score and introduced the concept of Constructability Score. The aim was to encourage designers to deliver more buildable designs upstream and builders to switch to more labour-efficient construction processes downstream.
Additional productivity roadmaps and codes were introduced subsequently, including the second Construction Productivity Roadmap in 2015, Construction Industry Transformation Map (ITM) in 2016 and Code of Practice on Buildability. These initiatives were means to achieve a highly integrated and technologically advanced construction sector by 2020.
The Journey
Locally, a series of social political reasons spurred the nation’s move, including:
- Our high dependence on cheap foreign workers;
- Overcrowding with close to 6 million in population; and
- The 2013 Little India riots in a largely peaceful society.
Due to a need to keep up with the demand for high-rise affordable housing for a rapidly growing population, there is further pressing need to increase productivity sustainably.
As with any disruptive workflow, policies were introduced to ease firms and practitioners towards the adoption of new technologies. Disincentives were introduced through the systematic increment of the Foreign Workers Levy (FWL) and reduction of Man-Year Entitlement (MYE) over time to neutralise the “cheap” component of foreign labour. Incentives were also introduced to encourage the industry to be early adopters of Building Information Modelling (BIM) tools and processes, for example.
Under the roadmap and ITM, the digital adoption started with government funding for hardware upgrades and software procurement and usage at individual firm level, to mandatory use of BIM model for building plan submissions for approval at government level. With the maturity in proficiency of the industry in BIM knowledge, Virtual Design and Construction (VDC) was introduced as a means to manage a BIM project’s process of construction. Integrated Digital Delivery (IDD), which builds on BIM and VDC, was launched shortly afterwards to help BIM-ready firms to build up collaboration capabilities.
The speed at which technology was implemented presented a steep learning curve for players in the industry. Reasonable progress was made – players with suitable projects adopted VDC and IDD, documenting productivity of the processes – but were largely confined to leading firms and early adopters.
At RLB, we embarked on our BIM journey as early as 2012 with the upgrade of hardware and investment in relevant BIM software. By 2014, we teamed up with the designers and developer to pilot the VDC framework for a 1,400-unit residential project. For pre-tender, we were able to reduce time taken to take off quantities and prepare tender documents by 30%. In post-contract stage, utilising the latest BIM model with tagged measurement schedule to certify monthly progress claims improved our productivity by 50%.
For downstream application, with the aid of BIM visualisation, modular construction offsite is increasingly being adopted to shorten overall construction time and improve productivity on-site. Prefabricated bathroom units (PBU), prefabricated prefinished volumetric construction (PPVC), prefabricated systems and MEP modules are cast and assembled off-site, usually in Malaysia and China, before they are transported to site in Singapore for just-in-time installation.
The implementation of the Regulations coincided with the completion of the integrated resorts in 2010/2011 and the concurrent cooling of the tender prices from its peak in 2008. Between 2011 and 2019, the year-on-year tender price movements remained more controlled despite mounting pressure from rising labour costs and an overhaul in work processes including investment in new technology. This points to an equilibrium in supply and demand within the market.
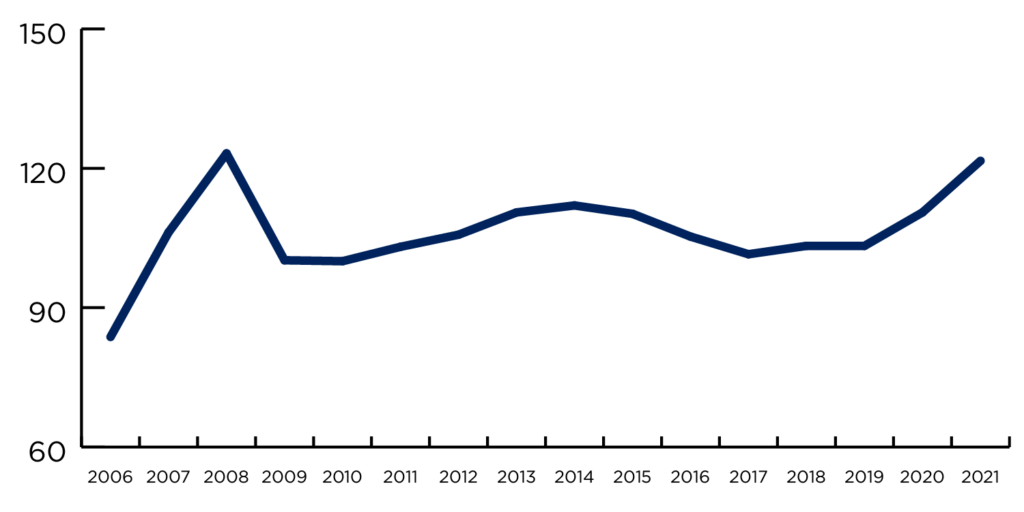
Graph 1: RLB Tender Price Index from 2006 to 2021
The Present
Tender prices in early 2020 were projected to maintain its equilibrium in the medium term despite geopolitical tensions and civil unrest in the region. However, the COVID-19 pandemic hit the Southeast Asian region in February 2020, triggering a series of lockdowns within and between national boundaries. The COVID-induced lockdown served as impetus for nationwide digital adoption such that the economy could continue functioning even in isolation.
With Information Communication Technology infrastructure and systems in place having embarked on ITM since the early 2010s, the majority of the society, including designers and quantity surveyors, was able to transit immediately to working from home, home-based learning, telecommuting and e-commerce. In contrast, the labour-intensive construction work saw productivity ground to a halt when worksites shut and a slow restart when worksites reopened.
Singapore, in particular the foreign workers who lived at dormitories, was hard hit by the pandemic. With foreign workers leaving Singapore due to a variety of reasons (fear of the pandemic, expiry of their work passes, etc.) and borders restrictions around the world in place, work permit holders in the Construction, Marine Shipyard and Process (CMP) sectors dropped by nearly 20% since the onset of the pandemic.
The manpower crunch has resulted in massive poaching among contractors which were under pressure to make up for the delay in their projects. Labour costs have spiked by 20% to 50% as demand exceeded supply, resulting in a spike in tender prices in 2020. Labour shortages persists even in its third year as waves of COVID-19 variants hit worldwide, causing border restrictions to tighten intermittently and render supply unreliable.
Spikes in demand and cost of labour reaffirmed the need for industry transformation through the adoption of technology such as Design for Manufacturing and Assembly (DfMA) to reduce our vulnerability to manpower disruptions. DfMA promotes offsite fabrication, which helps to reduce the number of workers on-site and make on-site segregation of workers easier, in order to adhere to safe management measures.
With epidemiologists warning of pandemics like COVID-19 becoming more frequent and deadlier, disruptions as a result of this pandemic are likely to recur if the industry does not change. Current solutions include a two-pronged approach of:
- Better risk management by changing contract conditions to cater for extension of time and cost claim due to future pandemic/ epidemic.
- More IDD drive to further apply BIM for construction, including developing the Common Data Environment (CDE) data standard.
A CDE allows project teams to create, organise and share information to foster collaboration, make timely decisions and take early interventions during the project’s delivery and building maintenance lifecycle.
The Future
While the pandemic has acted as a catalyst to hasten technological adoption, the momentum will also continue to pilot the shift in the industry faster than in the last decade. Blockchain, Data Analytics, Artificial Intelligence, and Virtual Reality will be the new norm in the industry. A new workforce is needed, some job re-designs required, in order to transform into a more productive industry characterised by high technology and lesser reliance on foreign labour.
Having benefited from the adoption of new technologies within our office, RLB is a strong proponent of staying ahead of the curve to offer more, without compromising on quality. We have set up a digital workgroup to drive our digital roadmap and guide our transition into the new era at the turn of the last decade. Since then, our staff have gone from understand BIM and its benefits to directly benefiting from the change.
We believe that stakeholders and companies that lag behind will lose out in the long run. Change, whilst uncomfortable, does bring forth new opportunities.
更多信息: