The number of considerations that go into starting a construction project are almost too numerous to count. Contracts, materials, labor, deadlines, even weather, to name a few.
They vary from project to project and any one of them can change in an instant, whether it be materials suddenly in short supply, labor that isn’t available for your particular kind of project (is it luxury hospitality or affordable residential?), or an unexpected phenomenon like Covid that makes everything suddenly screech to a halt.
Key to surmounting any problems that arise is being up to date on the state of each of the variables and where to go for replacements or replenishments if necessary. Be aware of added costs for any scenario that might play out—for example, if the funds will be needed (and available), or if the design might have to be changed.
Know Your Workforce
At the top of that list is the local work force. The design and construction team needs to know if it is robust enough and whether available workers have the requisite skills to get the job done. That means anything from hanging drywall to doing something specialized like pouring terrazzo or the unusual task of fabricating a dome for a new mosque. One-offs like massive art installations in commercial or hospitality projects can be particularly problematic without enough lead time.
Labor needs shift with booms and busts in the economy and projects can suffer if they get caught short of skilled labor. Hawaii, for example, experienced a huge boom in luxury high-rise construction in 2014-2015 when towers were popping up all over the place. Developers found themselves in a tough situation where drywall labor was capped out.
In other words, there was a back-up of projects and only a finite number of drywall installers available locally. Same thing with installers of windows and curtain walls – there just weren’t enough to do the jobs on schedule. Labor had to be flown in from inland locations, paid more and put up in hotels.
In such instances, project managers have to be flexible and knowledgeable enough to do what they have to do, which is hire labor from elsewhere. In Hawaii, for instance, this means getting labor either from one of the other islands or the mainland. This can have an environmental as well as financial impact, especially in a place like Hawaii where the shortage can be particularly acute.
There are unseen and unanticipated problems that come with this kind of demanding work schedule. While it’s good for the economy and laborers’ incomes, it often results in serious worker burnout. Everyone working longer hours, including weekends and holidays, leads to shortened careers while others make dramatic career path shifts based on burnout. It’s a real challenge that needs to be managed better industry-wide and especially significant during the “Great Resignation”.
Anticipate Potential Increased Workforce Costs
Increased cost is sometimes the hardest thing to reconcile. In the 2014-2015 example, the total cost of construction goes up as much as 10% if you fly workers in from the mainland or from destinations that are more than four hours’ drive time away. Project managers also have to calculate the cost of housing the workers, which can be substantial, and the fact that they might be slower given the lack of familiarity with the local market.
Situations like this don’t happen that often but when they occur, it becomes a huge topic of conversation and a huge concern among project managers and workers. There’s no question that a lack of available labor means the cost of the project is going to go up; you’ll be paying premiums on overtime until you hit a point where not even that will satisfy demand.
Skilled Labor And Specialty Projects
Project managers know that incurring additional costs where specialty projects are concerned is a given. Hiring workers with special, costlier skills is acceptable, as long as the cost is built into the design budget, like an art installation in a two- to three-story-high glassed-in lobby, or a golden dome for a mosque project in Louisville that was fabricated in Cincinnati, Ohio, and completed just weeks before the start of the Ramadan holiday. Labor can be even more complicated if you need to find a fabricator who could build to strict religious standards as well as the client’s.
Terrazzo flooring is another unusual material that requires a special skill set to lay down properly. Terrazzo specialists are rare in some locations, so the design team needs to be aware of the potential costs involved. But most designers and architects who know local markets rely on concrete aggregates that are attractive in their end use and readily available. The local labor force may be familiar with alternates, narrowing the margin of error.
They are also aware, for instance, of how cement can be manipulated to mimic other finishes with more of a high-end look. Same material, just a different way of polishing it. What workers and project managers know is that it’s about achieving a look with what’s already available and doing so at a reasonable price.
Perhaps peculiar to coastal regions, workers know code required designs for windows or curtain walls that give way in a flood. They’re rarer in Hawaii than in other coastal spots in the US, but that technology saves millions of dollars in damages when done properly, as the local work force knows how to perform the scope.
The local work forces in some states are also up on environmental concerns like solar panels which most agree are not as common as they could be. There have been government backed incentives to install them on residences creating savings on electric bills. The environmental impact of construction benefits by making the best use of locally available product and labor in any project.
Money savings from energy conservation initiatives in any kind of project generally get funneled back into the project to add more curb appeal to anything being built in what is an extraordinarily busy and booming residential and commercial market. Any money saved on commercial projects will likely go into upgrading mechanical or electrical plants to enhance efficiency. New methods tend to scare people – no one wants to be the guinea pig. But a sure thing is a product or technology that blows people away or carries a cost savings, either up front or long term, that is enticing enough to get them to take on the risk of the unknown or new technology. Project managers must be on top of new developments to know how to sell them.
As Seen In Building Design + Construction, October 2022, “Project Managers: Know Your Workforce
FURTHER INFORMATION:
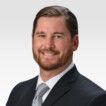